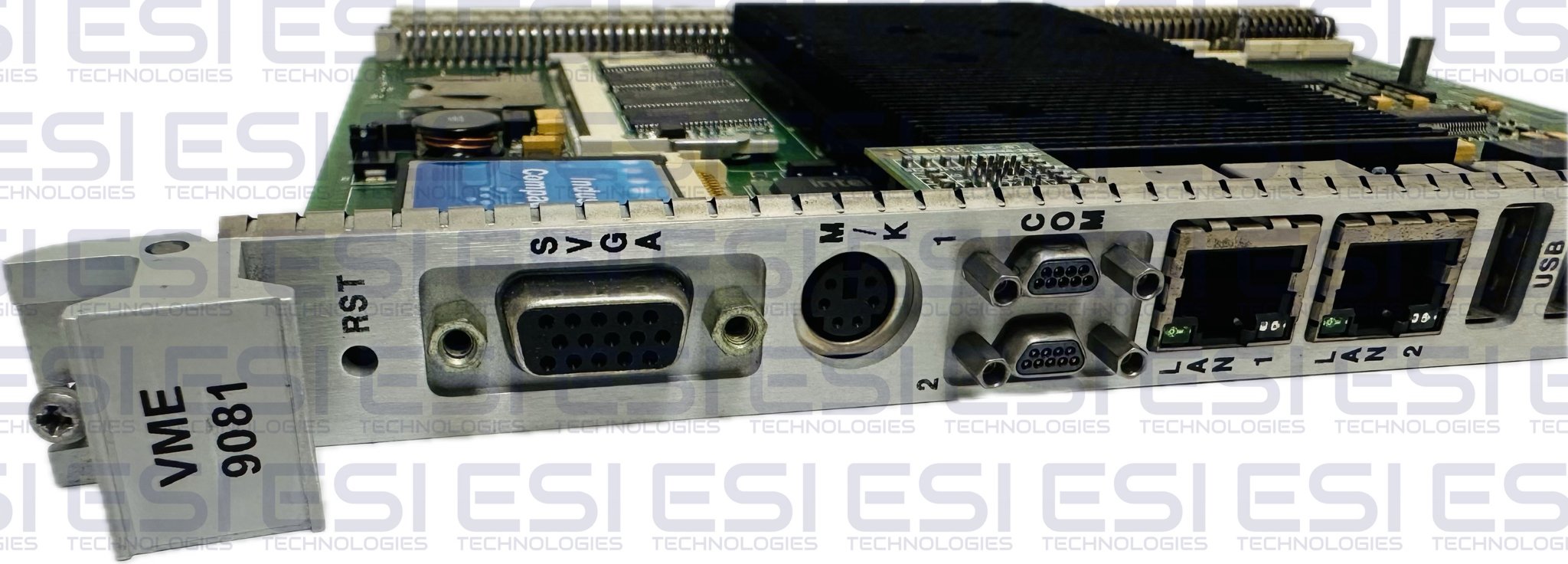
VMIVME-9081, VME-9081, VMIVME9081, VME9081
VMIVME-9081, VME-9081, VMIVME9081, VME9081
Product Specifications
-- Abaco’s Reflective Memory (5550, 5576, 5565 and 5588)
-- 10/100 Mbit Ethernet
-- Embedded (IIOC as slave CPU)
Firmware provides all required support for scanning inputs,
updating outputs, EU and data-type conversions, fault
detection, fault isolation, and error reporting
Optional host software support utilities
-- I/O point manager
-- Report generator
-- Configuration downloader
-- Real time interface software
-- Source code available in C
Supports a wide variety of Abaco’s General Purpose I/O
Boards
Available CRT-based control panel
Low cost expansion
Manufactured by Abaco Systems. Refurbished in good condition. The VMIVME-9081* provides a flexible, compact solution including user-friendly software utilities for the user who requires I/O products coupled with a preprogrammed single board computer (SBC) for effective turnkey operation. Multiple VMIVME-9081 can reside on a single Reflective Memory (RFM) link. Abaco provides a complete product line of I/O interface equipment designed specifically for the simulation and training industry. This equipment utilizes state of the art building blocks organized around the VMEbus architecture, providing a high density, high throughput, low cost solution to the I/O control problem. The real time interface equipment includes an Intelligent I/O Controller (IIOC) that is designed to operate in parallel with customer-furnished/programmed SBCs and other customer-furnished hardware. Abaco’s I/O board-level product line, trademarked BITMODULES*, is comprised of digital input/output boards, analog input/output boards and synchro/resolver input/output boards. Some of Abaco’s products are designed with extensive Built-in-Test capability and a front panel Fail LED to enable quick fault detection and isolation. These products support both offline and real time fault detection and isolation. Abaco’s real time interface equipment supports configuration data, generated by a customer-furnished host computer, that allows user-definable scan lists, data conversion formats and service order of each I/O type.
The system is expandable through the use of building block board-level products. As requirements change, the I/O system can be easily reconfigured. This configuration concept allows independent mapping of I/O points to memory, thus enabling the hardware configuration to change without changing the software interfaces. The system provides extensive data type and engineering unit conversions. Digitals may be represented as bit, byte, word or longword logical. In addition, the host’s definition of logical true may be designated as least significant bit (LSB) on, most significant bit (MSB) on or all bits on for byte, word and longword digital points. Analog and synchro values may be represented as host floating-point format or integer numbers. Engineering unit conversions for analogs include: offset binary, scaled, first-, second- and third-order polynomial, two’s complement integer, sine, cosine, arcsine, arccosine, table lookup, natural log and common log. Engineering unit conversions for synchros include: offset binary, degrees +180 to -180, degrees 0 to 360, scaled bipolar, unscaled unipolar and first-order polynomial. The system supports an available user-friendly CRT-based control panel that allows an engineer or maintenance technician to monitor all I/O points during real time, examine and modify all I/O points in nonreal-time and initiate and control offline diagnostics. The control panel can also display the current status of the system, errors found during real time or offline diagnostics and the current system configuration. The control panel provides a maintenance and test interface that will facilitate integration and checkout of the I/O system independent of other customer furnished/programmed hardware. Abaco’s real time I/O configuration can be organized as a star network, as shown in Figure 1. The central node of the I/O subsystem is the IIOC, responsible for all communications, CRT control, data format, engineering unit conversion and communication with the satellite or slave nodes. The slave nodes contain the I/O boards. For small I/O systems (less than 14 boards; approximately 900 digital points), only the IIOC chassis is required. Although the IIOC is designed to support up to 12 slave chassis, typical applications will involve only one to three chassis including the master chassis. Each slave node supports up to 19 I/O boards. Abaco’s high performance VMEbus multidrop repeater link (VMIVME-5504L*) provides a 32-bit parallel data path between the IIOC and a slave node up to 50 feet from the IIOC, reducing cable requirements and cost.
SKUE26
Qty 1
Alternative P/N #: VMIVME-9081, VME-9081, VME 9081, VMIVME 9081, 332-9301007700